Hazard and Risk
Management Procedures
1982
ACT
INFORMATION
OFFICIAL
THE
UNDER
RELEASED
Procedure Owner: General Manager, Human Resources
Approved by:
Date Last Reviewed: March 2016
Date of Next Review: March 2018
1
link to page 2 link to page 3 link to page 3 link to page 5 link to page 7 link to page 8 link to page 8 link to page 8 link to page 10
Hazard and Risk Management Procedures
These procedures are to be read in conjunction with WorkSafe New Zealand’s Hazard
and Risk Management Policy.
Introduction
Overview of Hazard and Risk Management Process Identifying Hazards
Assessing the Risk
1982
Controlling the Risk
Evaluating the Effectiveness of Controls
Monitoring and Review
Recording Identified Hazards – Hazard Registers
ACT
Hazard Identification and Risk Assessment Form
Introduction
WorkSafe has developed a hazard identification and risk management framework to
support the effective management of risks to health, safety and wellbeing, and of the
hazards that create those risks.
At an organisational level, our register will detail all of the significant organisational-level
risks and hazards, that is, those that impact on the majority of WorkSafe personnel
regardless of location or function. This register will be maintained nationally by the
INFORMATION
Principal Health and Safety Advisor.
Supporting the organisational register are functional and site-based registers. The
functional registers will detail the hazards and risks that only impact on personnel
working in a specified function. Each of these registers will be maintained nationally by
the designated functional owner. Functional registers are maintained for:
OFFICIAL
• Forestry – Owner: Chief Inspector, Assessments, Southern
• Agriculture – Owner: Chief Inspector, Assessments, Central
• Construction Owner: Chief Inspector, Assessments, Northern
•
THE
Manufacturing – Owner: Chief Inspector, Assessments, Northern
• Adventure Activities – Owner: Chief Inspector, Assessments, Central
• Energy Safety – Owner: Manager, Energy Safety
• Major Hazard Facilities – Owner: Deputy Chief Inspector Major Hazard Facilities
• Mining and Extractives – Owner: Chief Inspector Extractives
• Petroleum and Geothermal – Owner: Deputy Chief Inspector Petroleum and
UNDER
Geothermal
• Office-Based Work – Owner: Principal Health and Safety Advisor
Site registers will detail the hazards and risks specific to a particular WorkSafe site and
will be maintained by the Site manager.
This hierarchy of risk management will ensure the consistent treatment of common
hazards and risks nationally, will avoid duplication, and will enable nationally consistent
approaches to the control and management of these hazards and risks to be developed
RELEASED
and deployed.
Procedure Owner: General Manager, Human Resources
Approved by:
Date Last Reviewed: March 2016
Date of Next Review: March 2018
2
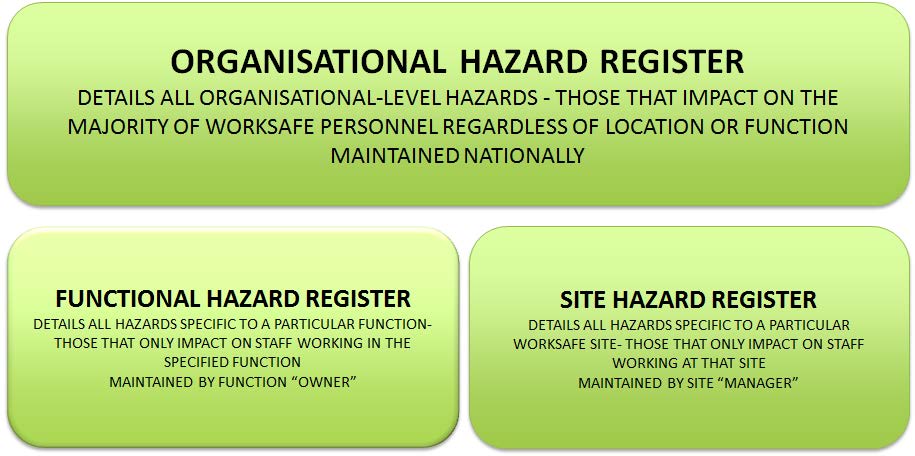
1982
ACT
Overview of Hazard and Risk Management Process
The flowchart on the following page summarises the key steps in the hazard
identification and risk management process. More detail on each of these steps in this
process can be found in the subsequent pages of this procedure.
Identifying Hazards
INFORMATION
Hazards will be identified in a number of ways. Having multiple approaches to the
identification of hazards will ensure that all potential hazards are identified and their
risks effectively managed.
Hazards may be identified through: OFFICIAL
o
Work process/system analysis and review
o
Plant and equipment analysis and review
o
Building analysis and review
o
Incident and accident investigation
THE
o
Analysis of altered work environment
o
Concerns raised by workers, health and safety representatives (HSRs)
or others at the workplace
o
Workplace audits and inspections
o
Site risk analysis
Prior to any new or altered
UNDER work process being introduced, any new or altered plant or
equipment being introduced, any new building being purchased or leased, or any current
building being altered or reconfigured, a full risk analysis and assessment must be
undertaken to identify and control hazards. The manager leading the introduction of
new or changed processes, plant, equipment, or facility is accountable and responsible
for ensuring that this occurs.
RELEASED
Procedure Owner: General Manager, Human Resources
Approved by:
Date Last Reviewed: March 2016
Date of Next Review: March 2018
3

Advised to Manager and, where
Hazard Identified*
significant, the Principal Health
and Safety Advisor
Temporary Controls Put In Place to Make
Safe and Control Hazard
1982
Risks Associated with
Assigned for Further, Review,
Hazard Assessed
Assessment and Control to
“Owner”
ACT
Consider Hazard Controls
Using Hierarchy of Controls
INFORMATION
OFFICIAL
Apply Hazard Controls
THE
Monitor Effectiveness
Identify new or improved controls
Of Controls
and implement
UNDER
Periodic review of hazard identification and
risk management process
RELEASED
Procedure Owner: General Manager, Human Resources
Approved by:
Date Last Reviewed: March 2016
Date of Next Review: March 2018
4
Workers visiting sites other than those controlled by WorkSafe must undertake a site risk
analysis before entering the site. This is a dynamic risk assessment process that
includes review of information already available from previous visits to the site and
direct observation before entering the site. In cases where the risk level is unacceptable
Workers who identify an uncontrolled hazard that places them at an unacceptable level
of risk when carrying out their function should report it to their manager immediately
and, where appropriate, take steps to make the area safe and control the hazard until a
full risk assessment can be completed and appropriate controls are identified and
implemented.
1982
Assessing the Risk
Once a hazard has been identified through any of the processes detailed above, it must
ACT
be assessed to determine the level of risk using the Hazard Identification and Risk
Assessment Form in Appendix A of these guidelines. Managers are responsible for
ensuring that this occurs for all hazards identified by them, or notified to them.
Once this initial risk assessment has been completed and interim controls put in place to
minimise the risk, the form must be sent to the relevant ‘owner’ who is accountable for
reviewing the risk assessment, identifying and implementing controls, reviewing the
effectiveness of the controls implemented, entering the hazard on the appropriate
hazard register, and notifying Workers about the newly identified hazard and controls.
Each of these steps is detailed below.
INFORMATION
Hazard Owners:
• Organisational Hazards – Owner: Principal Health and Safety Advisor
• Functional Hazards
o
Forestry – Owner: Chief Inspector, Assessments, Southern
o
Agriculture – Owner: Chief Inspector, Assessments, Central
o
Construction - Owner: Chief Inspector, Assessments, Northern
OFFICIAL
o
Manufacturing – Owner: Chief Inspector, Assessments, Northern
o
Energy Safety – Owner: Manager, Energy Safety
o
Major Hazard Facilities – Owner: Deputy Chief Inspector Major Hazard
THE
Facilities
o
Mining and Extractives – Owner: Chief Inspector Extractives
o
Petroleum and Geothermal – Owner: Deputy Chief Inspector Petroleum
and Geothermal
o
Office-Based – Owner: Principal Health and Safety Advisor
• Site-specific Hazards – Site-based Assessment Manager, or, for National Office,
UNDER
Principal Health and Safety Advisor
WorkSafe uses a two-stage process to assess the level of risk in relation to identified
hazards. This involves an assessment of the likely consequence in encountering the
hazard identified, that is, how seriously someone could be hurt, and the likelihood, that
is, how likely it is that individuals would be hurt that severely, using a five point scale.
These two assessments are then combined to establish an overall risk rating, which then
influences the actions that must be taken in controlling the hazard. This is detailed on the
RELEASED
following page. This assessment must be undertaken by the hazard owner and recorded
on the Hazard Identification and Risk Assessment Form.
Procedure Owner: General Manager, Human Resources
Approved by:
Date Last Reviewed: March 2016
Date of Next Review: March 2018
5
Consequence: How Severely Could Someone Be Harmed?
Consequence Descriptor
☐
Critical
Death or permanent disability
☐
Major
Serious injury or illness, hospital treatment
☐
Moderate
Injury or illness requiring medical treatment and some lost
time
☐
Minor
Minor injury or illness, first aid only required
☐
Insignificant Injury or illness requiring no treatment or first aid
1982
Likelihood: How likely is it Someone Could be Harmed?
ACT
Likelihood
Descriptor
☒ Certain to
Expected to occur in most circumstances
Occur
☐ Very Likely
Will probably occur in most circumstances
☐ Possible
Might occur occasionally
☐ Unlikely
Could happen some time
☐ Rare
May happen only in exceptional circumstances
Risk Assessment
INFORMATION
Likelihood (L)
Consequences (C)
Rare
Unlikely
Possible
Very High
Certain
Critical
moderate
moderate
high
extreme
extreme
Major
OFFICIAL
low
moderate
high
high
extreme
Moderate
low
moderate
high
high
high
THE
Minor
low
low
moderate
moderate
moderate
Insignificant
low
low
low
low
moderate
UNDER
Assessed Risk
Description of Risk Level
Actions
Level
☐
Low
If an incident were to occur, there would be
Activity can be taken.
little likelihood that an injury or il ness would
result.
☐
Medium
If an incident were to occur, there would be
Controls may be needed.
some chance that an injury or il ness would
result
RELEASED
☐
High
If an incident were to occur, it would be likely
Controls wil need to be in place before
that an injury or il ness requiring medical
the activity is undertaken
Procedure Owner: General Manager, Human Resources
Approved by:
Date Last Reviewed: March 2016
Date of Next Review: March 2018
6
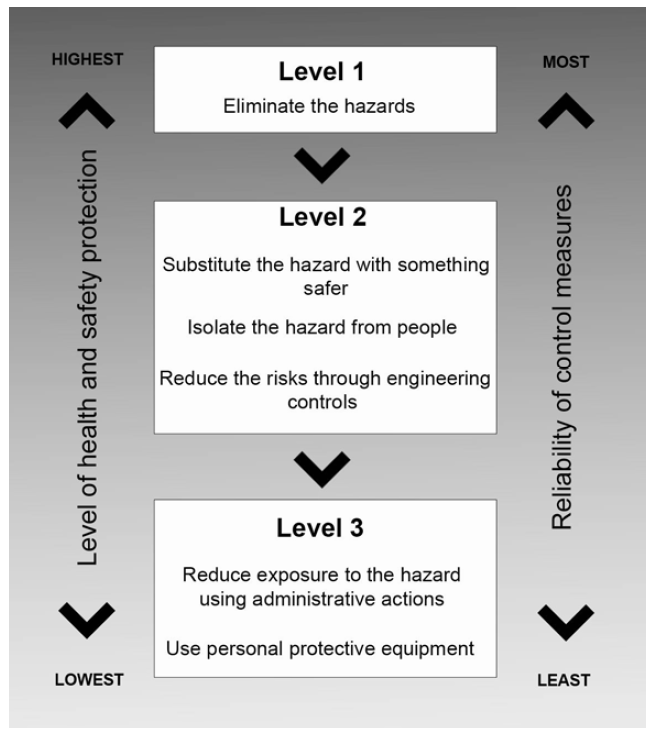
treatment would result.
☐
Extreme
If an incident were to occur, it would be likely
Consider alternatives to doing the
that a permanent, debilitating injury or il ness,
activity. Significant control measures
or death would result
must be implemented before the
activity is undertaken.
Controlling the Hazard
Where the risk assessment identifies that controls either may be needed or must be in
place, then steps must be taken to identify and implement appropriate controls.
1982
Temporary controls may be put in place until more comprehensive controls can be
developed and implemented. The hierarchy of risk controls must be used to identify and
implement appropriate controls, both temporary and ongoing. The hierarchy of risk ACT
controls will assist in identifying the most effective controls to manage the risk
associated with the hazard.
Hierarchy of Risk Controls
INFORMATION
OFFICIAL
THE
UNDER
Firstly, consideration should be given as to whether the hazard can be eliminated. If it
can, then this should occur.
If the hazard cannot be eliminated, then consideration should be given to substituting
the hazard with something safer. If this cannot be done then consideration should be
given to isol
RELEASED ating the hazard from people. If this is not possible, then consideration
should be given to reducing the risks through engineering controls.
Procedure Owner: General Manager, Human Resources
Approved by:
Date Last Reviewed: March 2016
Date of Next Review: March 2018
7
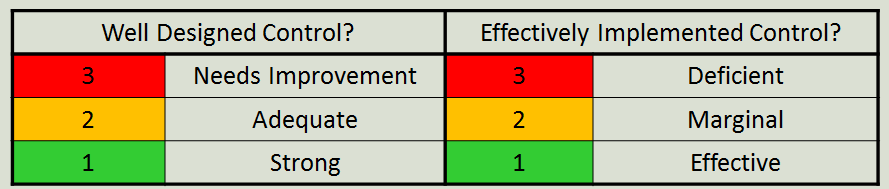
If it is not possible to apply either level 1 or level 2 controls, then exposure to the hazard
must be reduced using administrative actions and/or personal protective equipment. A
combination of level 2 and level 3 controls may be appropriate to manage the risk.
The provision of training and/or education should also be provided to support and
enhance the effectiveness of the controls that are put in place to manage the hazard.
Controls and training implemented to manage the risk must be recorded on the Hazard
Identification and Risk Assessment Form.
Evaluating the Effectiveness of Controls
1982
Where controls have been implemented, they must be reviewed periodically to evaluate
their effectiveness. This will enable WorkSafe to determine whether additional controls
or action is necessary. The evaluation will consider whether the control is well designed
ACT
and whether it is effectively implemented.
The effectiveness of hazard controls will be reviewed annually, or more frequently where
accident/incident data suggests this is necessary. Hazard owners are responsible for
undertaking this review. The outcomes of the most recent review must be recorded on
the Hazard Identification and Risk Assessment Form.
INFORMATION
Monitoring and Review
The hazard owner is also responsible for identifying and actions and activities that are to
be undertaken to monitor the hazard/risk, and the effects of exposure to the hazard.
OFFICIAL
This is also to be recorded on the Hazard Identification and Risk Assessment Form.
Recording Identified Hazards – Hazard Registers
THE
The hazard owner is responsible for maintaining the hazard identification and risk
assessment forms for all identified hazards in their area of responsibility, for updating
the relevant hazard register when new or changed hazards are identified and notified to
them, and for ensuring that all Workers potentially affected by the hazard are advised of
its existence and of the controls that are in place to manage the risk. All Workers are
UNDER
responsible for maintaining an up-to-date knowledge of the hazards that have been
identified within their area of work (organisational, functional and site) and for complying
with the controls that are put in place to manage the risk associated with those hazards.
The organisational, functional and site-specific hazard registers are published on the
WorkSafe intranet site, and can be accessed here.
Process for reporting hazards
RELEASED
Procedure Owner: General Manager, Human Resources
Approved by:
Date Last Reviewed: March 2016
Date of Next Review: March 2018
8
When an uncontrolled hazard is identified, or it is believed that the existing hazard
controls are inadequate; the responsible manager will complete the risk assessment
process set out in these procedures. Completed forms will be directed to the Principal
Health and Safety Advisor for consideration. The Principal Advisor will review the risk
assessment as is necessary and will assign to the appropriate risk “owner” to ensure
necessary risk mitigation is implemented. The risk “owner” is also responsible for
amending, as necessary, the relevant risk register. Risk “ownership” is as detailed
previously regarding organisational, function and site risks.
Scheduled risk management activities
1982
An annual schedule of review will apply to our hazard and risk management activities,
notwithstanding that, in addition to the annual schedule, there will be a need to review
ACT
hazard and risk assessments and registers at other times, when work practices change,
when new work practices are introduced, investigations, audits etc.
July
Site review of all hazards, risk assessment and controls
July
Functional review of hazards, risk assessment and controls
August
Hazard registers reviewed to reflect site and functional reviews
August
Organisational review of hazards, risk assessment and controls
September
H&S annual activity planned INFORMATION
November
CE/SLT Sign-off of registers and plan
OFFICIAL
THE
UNDER
RELEASED
Procedure Owner: General Manager, Human Resources
Approved by:
Date Last Reviewed: March 2016
Date of Next Review: March 2018
9

APPENDIX ONE – HAZARD IDENTIFICATION AND RISK ASSESSMENT FORM
Hazard Identification
and Assessment Temp
1982
ACT
INFORMATION
OFFICIAL
THE
UNDER
RELEASED
Procedure Owner: General Manager, Human Resources
Approved by:
Date Last Reviewed: March 2016
Date of Next Review: March 2018
10